What Is in Control System
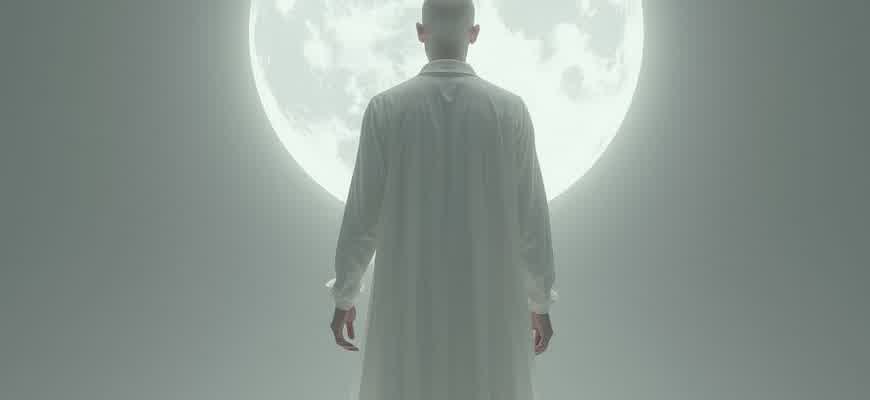
A control system is a set of interconnected components designed to manage the behavior of other devices or systems. These systems can be categorized into two main types: open-loop and closed-loop systems. The primary goal is to regulate the output of a system based on inputs, ensuring desired performance levels are achieved.
The key elements of a control system include:
- Controller: The component that processes input signals and generates output commands to control the system.
- Sensor: A device that measures the system's output and provides feedback to the controller.
- Actuator: A mechanism that influences the system based on controller commands.
- Process: The part of the system that undergoes regulation, often involving physical or chemical operations.
"A control system works by continuously adjusting its components to maintain the desired output, either automatically or with human intervention."
In the case of a closed-loop system, the output feedback is continuously monitored and used to correct the system's performance. This feedback mechanism allows for self-regulation, providing accuracy and stability in dynamic environments.
Below is a table summarizing the components:
Component | Function |
---|---|
Controller | Processes input signals and generates output commands. |
Sensor | Monitors the output of the system and provides feedback. |
Actuator | Executes actions based on commands from the controller. |
Process | The part of the system being regulated or controlled. |
Understanding the Basic Components of a Control System
A control system is designed to manage and regulate the behavior of other systems, ensuring that they perform in a desired manner. It involves a set of interconnected elements that work together to monitor, adjust, and direct the system’s performance. The key components are responsible for continuously receiving feedback, analyzing it, and making necessary adjustments to maintain control over the system's state.
At the core of any control system lies a structure that includes input, process, and output. Each element has a specific role in ensuring the system operates efficiently and according to set parameters. By understanding the purpose and function of each component, we can better appreciate how the system achieves stability and control over complex processes.
Key Components
- Sensor: Detects changes in the system's environment or performance and provides feedback.
- Controller: Analyzes input from the sensor and makes decisions based on predefined criteria or algorithms.
- Actuator: Receives commands from the controller and implements the necessary changes to the system.
- Feedback Loop: Continuous information flow between the output and input to ensure the system adapts accordingly.
Process Overview
- Measurement: Sensors collect data regarding the system's performance.
- Analysis: The controller processes this data, compares it to desired setpoints, and decides if an action is required.
- Action: The actuator carries out the necessary adjustment to maintain or achieve the desired state.
- Feedback: The results of the actuator’s actions are fed back into the system, influencing future decisions.
The integration of these components ensures that the control system can make real-time adjustments and maintain stability even in dynamic environments.
Component Relationships
Component | Function |
---|---|
Sensor | Monitors the current state of the system and detects any deviations. |
Controller | Processes sensor data and generates control signals based on logic or algorithms. |
Actuator | Executes the necessary changes to the system based on control signals. |
Feedback Loop | Provides real-time data to continuously adjust and refine the system's operation. |
How Control Systems Are Applied in Manufacturing Processes
Control systems play a critical role in modern manufacturing processes by enabling precise regulation and automation of various operations. From assembly lines to complex production setups, these systems ensure that production runs smoothly, efficiently, and with minimal human intervention. By integrating sensors, actuators, and feedback loops, control systems help to maintain the desired quality and performance of the manufacturing process.
In manufacturing, control systems are applied to monitor and adjust parameters such as temperature, pressure, speed, and material flow. This allows for consistent product quality, reduced waste, and optimized use of resources. The use of advanced control techniques like PID (Proportional-Integral-Derivative) controllers ensures that any fluctuations or deviations in production are corrected in real-time, leading to higher throughput and lower defect rates.
Types of Control Systems in Manufacturing
- Open-loop Control: Does not use feedback to adjust the process, making it suitable for processes where output does not vary significantly.
- Closed-loop Control: Uses feedback to continuously adjust inputs, ensuring more precise control over the process.
- Distributed Control Systems (DCS): A system that distributes control across various controllers connected through a network, often used in complex processes like chemical manufacturing.
Common Applications in Manufacturing
- Automated Assembly Lines: Control systems regulate the speed, positioning, and synchronization of robotic arms and conveyors, ensuring products are assembled with high precision.
- Temperature Control: In industries like plastics and metals, control systems maintain optimal temperature levels to ensure uniformity in material properties and prevent defects.
- Quality Control: Automated inspection systems monitor product quality by detecting deviations from specifications, reducing human error.
Control systems in manufacturing are crucial for improving efficiency, product quality, and reducing operational costs. They ensure that complex processes can be automated and optimized without constant human supervision.
Example of Control System in Manufacturing Process
System | Application | Advantages |
---|---|---|
PID Controller | Maintaining consistent temperature in injection molding machines | Improved accuracy, reduced temperature fluctuations, better product quality |
PLC (Programmable Logic Controller) | Automating assembly line for automotive parts | Increased flexibility, real-time monitoring, easy integration with sensors |
Key Differences Between Open-Loop and Closed-Loop Control Systems
Control systems play a crucial role in various applications, ensuring that processes behave as desired. They can be categorized into open-loop and closed-loop systems based on their feedback mechanisms. Open-loop systems operate without any feedback, meaning they do not adjust their operations based on output conditions. In contrast, closed-loop systems incorporate feedback, allowing for continuous monitoring and adjustment of the system to maintain the desired performance.
The key distinction between the two types lies in their use of feedback for regulating output. While open-loop systems are simple and faster in terms of execution, closed-loop systems are more complex and accurate due to their ability to adjust dynamically in response to changing conditions.
Open-Loop Control System
- No feedback is used to adjust the system.
- Operates based on predetermined inputs and settings.
- Simple and faster execution.
- Less accurate, especially in the presence of disturbances or changes in conditions.
- Commonly used in systems where high precision is not critical, like washing machines.
Closed-Loop Control System
- Utilizes feedback to adjust the system output continuously.
- Monitors output and corrects any deviation from the desired result.
- More complex and typically slower due to feedback processing.
- Highly accurate and reliable, even in changing conditions.
- Used in critical systems like thermostats or autopilot in aircraft.
Comparison Table
Characteristic | Open-Loop System | Closed-Loop System |
---|---|---|
Feedback | No | Yes |
Complexity | Simple | Complex |
Accuracy | Low | High |
Example | Microwave oven | Air conditioning system |
"Closed-loop systems provide better control and accuracy in dynamic environments, while open-loop systems are faster and easier to implement."
How Sensors and Actuators Drive the Functionality of Control Systems
Control systems rely heavily on sensors and actuators to maintain desired operations and ensure systems behave predictably. Sensors act as the eyes and ears of the system, constantly collecting data from the environment or machinery. This data is then processed and used by controllers to make decisions. Actuators, on the other hand, are responsible for taking those decisions and implementing physical actions to affect the system. Together, these components form a feedback loop that is critical to achieving precision in automated systems.
The seamless interaction between sensors and actuators enables control systems to respond dynamically to changing conditions. Sensors monitor variables such as temperature, pressure, and speed, and their input is essential for adjusting actuator behavior accordingly. Without accurate sensor data, the actuator's response may be inadequate, leading to inefficiency or failure in the system.
Key Functions of Sensors and Actuators
- Sensors: Measure environmental or system conditions and convert them into signals for processing.
- Actuators: Execute the system's response by converting control signals into mechanical or electrical actions.
- Control Loop: The sensor data is analyzed by the controller, which then sends signals to actuators to adjust system behavior.
Examples of Sensor and Actuator Interactions
- Temperature Control System: A thermostat sensor monitors room temperature and communicates the data to the controller. Based on the temperature threshold, the controller sends a signal to an actuator (e.g., a heating or cooling system) to adjust the temperature.
- Robotics: In robotic arms, position sensors track the arm's movements and relay data to the control system. The controller then sends precise instructions to actuators to position the arm as needed for specific tasks.
- Automated Manufacturing: Pressure sensors detect fluctuations in machine pressure, prompting actuators to adjust machinery to maintain optimal performance.
Important Considerations for Control Systems
Component | Function | Impact on Control System |
---|---|---|
Sensor | Measures variables (e.g., temperature, pressure) | Provides input data that drives system adjustments |
Actuator | Performs physical actions based on control signals | Executes system decisions, ensuring precise operation |
"The collaboration between sensors and actuators ensures that control systems can maintain stability, efficiency, and adaptability in dynamic environments."
Integrating Control Systems with Modern IoT Technologies
Modern control systems are increasingly relying on the Internet of Things (IoT) to enhance their functionality, scalability, and real-time capabilities. IoT enables control systems to gather data from a vast network of interconnected devices, providing valuable insights for decision-making and optimization. This integration allows for smarter control and automation in industrial processes, buildings, transportation systems, and more.
The synergy between IoT and control systems introduces several benefits, such as remote monitoring, predictive maintenance, and adaptive control. By leveraging IoT sensors and actuators, control systems can interact with the physical world in a more dynamic and intelligent manner, enhancing overall system efficiency and reducing human intervention.
Key Components of IoT-Integrated Control Systems
- IoT Sensors: Devices that collect data such as temperature, pressure, and motion, feeding it to the control system for analysis.
- Connectivity Protocols: Communication standards (e.g., MQTT, HTTP) used for transmitting data between IoT devices and control systems.
- Cloud Platforms: Platforms that store and process data from IoT devices, allowing control systems to access and analyze it remotely.
- Edge Computing: The use of local processing units to reduce latency and handle data analysis closer to the data source.
Challenges and Considerations in Integration
- Data Security: IoT devices can be vulnerable to cyberattacks, so strong security measures are essential to protect both control systems and IoT networks.
- Interoperability: Integrating legacy control systems with modern IoT technologies can be challenging due to compatibility issues between older and newer technologies.
- Data Overload: IoT generates vast amounts of data, which can overwhelm control systems if not properly managed and filtered.
Benefits of IoT Integration in Control Systems
Benefit | Description |
---|---|
Improved Efficiency | Real-time data from IoT devices allows for better decision-making and faster response times in control processes. |
Cost Reduction | Predictive maintenance enabled by IoT reduces downtime and maintenance costs for industrial systems. |
Scalability | IoT technologies provide the flexibility to scale control systems without the need for major hardware upgrades. |
"Integrating IoT with control systems is transforming industries by enabling smarter, more efficient operations through real-time data and automation."
Choosing the Right Control System for Your Business Needs
Selecting the optimal control system for your organization is a critical step toward enhancing operational efficiency. A well-designed system not only streamlines processes but also allows businesses to respond faster to changes in the market and internal dynamics. It is essential to understand the specific requirements of your business, its scale, and the complexity of its operations when choosing the right solution.
When evaluating potential control systems, consider the key factors that will impact the performance of your business. This includes scalability, ease of integration with existing infrastructure, real-time monitoring capabilities, and system reliability. It is also crucial to assess the support and training resources offered by the provider to ensure smooth implementation.
Key Considerations for Selecting a Control System
- Scalability: The system should grow with your business. Choose a solution that can handle future demands.
- Integration: Ensure the system can easily integrate with your existing machinery or software.
- Real-time monitoring: A good control system provides live data to make informed decisions on the fly.
- Cost-effectiveness: The system should offer a balance between cost and functionality.
Steps to Follow When Choosing a Control System
- Assess your business needs: Understand what problems you are trying to solve and how a control system can address them.
- Research available systems: Compare features, customer reviews, and technical specifications of different solutions.
- Test compatibility: Ensure the chosen system integrates with your current infrastructure.
- Calculate total costs: Factor in installation, training, and ongoing maintenance expenses.
- Implement and monitor: Once selected, carefully deploy the system and continuously monitor its performance to ensure it meets your expectations.
"The right control system not only improves efficiency but also strengthens your competitive advantage by providing real-time insights and adaptability."
Control System Comparison
Feature | System A | System B |
---|---|---|
Scalability | High | Medium |
Integration Ease | Easy | Moderate |
Real-time Data | Yes | No |
Cost | High | Low |
Common Challenges in Control System Implementation and Solutions
Control systems play a crucial role in ensuring the stability and efficiency of various automated processes. However, their implementation is often accompanied by several challenges that need to be addressed effectively to ensure the system's success. From integration issues to performance optimization, the process can be complex and demanding. Below are some of the most common challenges encountered during control system deployment and their corresponding solutions.
One of the major challenges in control system implementation is dealing with hardware and software integration. Discrepancies between the components or software incompatibilities can lead to system malfunctions, reducing reliability and performance. Inadequate testing and calibration also contribute to inconsistent behavior, leading to unstable outputs.
Key Challenges and Solutions
- Integration and Compatibility Issues: Ensuring that hardware and software components work together smoothly can be difficult, especially when using off-the-shelf parts or software from different vendors.
- System Stability and Performance: Instabilities in control loops due to poor tuning or noisy inputs can degrade system performance, leading to errors and failures.
- Real-time Data Processing: Delays in processing real-time data can cause the system to become unresponsive, particularly in fast-paced environments.
Solutions
- Thorough System Testing: Implementing rigorous testing protocols during development can identify potential integration issues early on. This includes unit tests, integration tests, and system tests to check both individual components and the system as a whole.
- Advanced Tuning Techniques: Employing sophisticated algorithms for control loop tuning, such as PID optimization, can help to stabilize the system and ensure smoother performance even in the presence of disturbances.
- Real-time Data Processing Enhancements: Upgrading hardware to support higher processing speeds or optimizing software to handle larger data volumes can help minimize delays and improve system responsiveness.
Note: Effective communication between the development team and end-users is critical for identifying real-world issues and ensuring that the system meets performance expectations.
Common Issues with Data Handling
Issue | Impact | Solution |
---|---|---|
Data Inconsistency | Can cause inaccurate control actions and reduced system reliability. | Implement robust error-checking algorithms and data validation techniques. |
Data Latency | Delays in data transmission can result in outdated control decisions. | Use faster communication protocols and reduce system complexity. |