5s Training Online Free
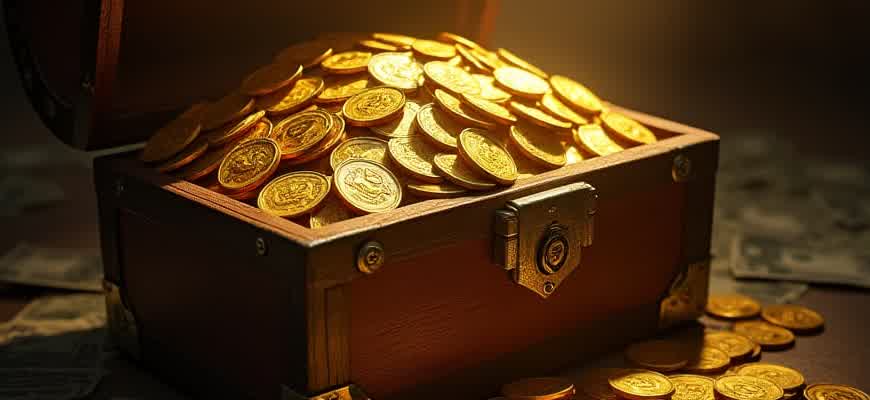
The 5S methodology is a powerful tool for improving workplace efficiency and safety. It involves organizing and standardizing work environments to reduce waste, increase productivity, and maintain order. This training offers a comprehensive introduction to the 5S principles, allowing individuals to learn and implement them without any cost. Below is a breakdown of the core concepts covered in free online courses for 5S:
- Sort – Eliminate unnecessary items from the workspace.
- Set in Order – Organize remaining items to be easily accessible.
- Shine – Regularly clean the workspace to maintain a safe and efficient environment.
- Standardize – Create consistent processes for maintaining the first three steps.
- Sustain – Develop habits to maintain and improve the system over time.
By participating in this online course, individuals will gain a clear understanding of each principle and how to implement them effectively in their workplace. The course structure typically includes:
- Introduction to 5S concepts and history.
- Practical examples and case studies.
- Quizzes to test knowledge and ensure comprehension.
- Certification upon successful completion.
“5S is not just a technique, but a way of thinking that enhances productivity and fosters continuous improvement in the workplace.”
Many organizations now offer free access to these courses to help employees implement 5S and improve operational efficiency. Enrolling in such programs can lead to better workplace organization, increased safety, and a significant reduction in waste.
Master 5S with Free Online Training: A Practical Guide
Learning the fundamentals of 5S methodology is essential for creating an organized, efficient, and safe work environment. By mastering these principles, individuals and organizations can significantly improve productivity and reduce waste. Fortunately, there are numerous free online resources that provide comprehensive training on 5S principles, helping you to implement these techniques without any cost.
This guide outlines how you can learn 5S through free online courses, offering you the tools to streamline your workplace. Whether you're new to the concept or looking to refine your understanding, there are plenty of accessible materials available to help you get started.
What is 5S?
5S is a lean management tool that focuses on organizing a workspace to improve efficiency. The five pillars are:
- Sort - Eliminate unnecessary items from the workspace.
- Set in order - Organize essential items for easy access.
- Shine - Keep the workspace clean and well-maintained.
- Standardize - Establish standardized practices for consistency.
- Sustain - Develop habits to maintain the improvements long-term.
Key Online Resources for Free 5S Training
Several online platforms offer detailed courses on implementing 5S in various settings. Here are some top options:
- Coursera - Offers free courses from universities that cover lean management and 5S techniques.
- edX - Provides free access to courses on productivity and workplace organization, including 5S principles.
- Udemy - Offers beginner-level courses on 5S, focusing on hands-on implementation and examples.
"Mastering 5S is not just about cleaning; it’s about creating a systematic, efficient process that becomes ingrained in daily work routines."
Key Benefits of 5S Training
Benefit | Impact |
---|---|
Improved Efficiency | Streamlines workflows, reducing time spent searching for tools and materials. |
Enhanced Safety | Reduces clutter, making the workplace safer for everyone. |
Cost Savings | Reduces waste and unnecessary spending by optimizing resources. |
By completing free online training, you’ll gain the knowledge to apply 5S in your workplace, boosting productivity and creating a culture of continuous improvement. Take advantage of these resources to learn at your own pace and start making impactful changes today.
How to Start Your 5S Journey with Free Online Resources
Beginning your 5S journey can seem overwhelming, but with the right resources, you can master this powerful methodology without spending a dime. Numerous online platforms offer free courses and materials to guide you through the essential principles of 5S, allowing you to improve workplace organization and efficiency. Whether you're a beginner or someone looking to enhance your existing knowledge, these resources can provide the foundation you need.
Free online courses and resources are abundant, from detailed instructional videos to downloadable e-books. These platforms break down each of the 5S principles–Sort, Set in Order, Shine, Standardize, and Sustain–into manageable modules, making it easier for you to understand and implement them in your workplace.
Free 5S Online Resources to Explore
- Coursera – Offers a variety of free courses related to workplace efficiency, including 5S principles.
- edX – Provides free access to several courses focusing on lean manufacturing and continuous improvement, including 5S training.
- YouTube – Features countless videos from industry experts demonstrating the practical applications of 5S.
- Lean.org – Offers free articles, guides, and resources specifically about 5S implementation.
Steps to Follow for Learning 5S Online
- Choose the Right Platform: Start by selecting an online platform that suits your learning style, whether it’s a structured course or free-form video tutorials.
- Understand the Basics: Familiarize yourself with the five principles of 5S through articles and videos. Make sure you understand what each step entails.
- Practice Through Case Studies: Look for case studies or examples of successful 5S implementations to see how the principles are applied in real-world situations.
- Implement Gradually: Apply the 5S steps to your workspace in phases, beginning with one principle at a time, such as sorting and organizing before moving on to sustainment.
- Seek Feedback: If possible, collaborate with others to get feedback on your 5S implementation. This can help identify areas for improvement.
Remember, 5S is not just about cleaning and organizing–it’s about fostering a culture of continuous improvement. Every small change can lead to big improvements in workplace efficiency.
5S Implementation Checklist
5S Principle | Key Action |
---|---|
Sort | Remove unnecessary items from the workplace to eliminate clutter. |
Set in Order | Organize tools and materials for easy access and efficiency. |
Shine | Ensure cleanliness and maintenance of workspaces to improve safety and morale. |
Standardize | Create standardized procedures to maintain consistency in the workplace. |
Sustain | Maintain the improvements by setting up regular audits and team involvement. |
Setting Clear Goals for Your 5S Training: What You Need to Focus On
To ensure the success of your 5S training, it's crucial to have well-defined objectives. These goals should guide the training process, helping participants understand the purpose of 5S and how to implement it effectively. The clearer the objectives, the more likely employees are to engage with the content and apply it in their day-to-day tasks.
Focus on outcomes that will have a tangible impact on your workplace. Set specific, measurable targets that align with the key principles of 5S. Below are key focus areas to guide your training efforts.
Key Areas to Focus On
- Understanding 5S Principles: Ensure that participants clearly understand the five core principles: Sort, Set in Order, Shine, Standardize, and Sustain.
- Practical Application: Provide real-world examples to help learners apply the principles to their work environment.
- Employee Involvement: Train participants on how to encourage team collaboration and continuous improvement.
- Measuring Progress: Focus on setting benchmarks and defining metrics for assessing the success of 5S implementation.
Measuring Success in 5S Training
To ensure that your training is effective, it's essential to establish clear criteria for success. This can be done through:
- Regular assessments and quizzes to evaluate knowledge retention.
- Feedback from employees regarding the usability of the 5S system in their work areas.
- Performance indicators such as improved productivity, reduced waste, and enhanced workplace safety.
Table: Example of Key Metrics for Measuring 5S Success
Metric | Target | Measurement Method |
---|---|---|
Workplace Cleanliness | 95% clean workstations | Regular cleanliness audits |
Waste Reduction | 10% reduction in waste | Tracking waste output before and after training |
Employee Engagement | 80% participation in 5S activities | Surveys and feedback forms |
Clear goals help both trainers and trainees stay focused on what truly matters, making the training process more efficient and impactful.
Steps to Implement the 5S Methodology in Your Workspace
The 5S methodology is a powerful tool to optimize the workplace by creating a more efficient and organized environment. It involves five key steps, each designed to systematically improve different aspects of your workspace. These steps help eliminate waste, reduce inefficiencies, and foster a culture of continuous improvement. By focusing on the essentials and eliminating clutter, businesses can boost productivity and create a more positive work environment.
To successfully implement 5S in your workspace, it is essential to follow a clear and structured approach. Below are the key steps to effectively introduce 5S into your daily operations:
1. Sort (Seiri)
Sorting is the first and most critical step in the 5S methodology. It involves identifying and separating essential tools and materials from those that are unnecessary. By eliminating non-essential items, you ensure that only the necessary resources are readily available, reducing clutter and improving efficiency.
2. Set in Order (Seiton)
This step focuses on organizing all remaining items in a logical and accessible way. Tools and materials should be stored according to frequency of use, ensuring that workers can quickly find what they need. A well-ordered workspace promotes smooth operations and minimizes the time spent searching for items.
3. Shine (Seiso)
Cleaning and maintaining the workspace is essential to keep the environment safe and functional. This step emphasizes regular cleaning routines, which not only ensure a tidy workspace but also prevent equipment breakdowns and improve overall workplace health and safety.
4. Standardize (Seiketsu)
Standardization involves creating procedures and guidelines to maintain the improvements made in the previous steps. Clear instructions for how tools, materials, and spaces should be organized help ensure consistency and continuity. This step helps sustain the benefits of the 5S process over time.
5. Sustain (Shitsuke)
The final step in the 5S methodology is to embed the practices into the company culture. It requires ongoing training and discipline to ensure that the improvements are consistently maintained. Regular audits and continuous reinforcement are crucial for sustaining the long-term effectiveness of 5S.
Important: Consistent leadership and employee engagement are essential to successfully implement and sustain the 5S methodology. Without commitment from all levels of the organization, the system is unlikely to be effective.
Implementation Process
- Train your team: Ensure everyone understands the principles of 5S.
- Assess the current state: Evaluate your workspace for areas of improvement.
- Begin with sorting: Remove unnecessary items to clear up space.
- Implement organization and cleanliness standards: Set clear procedures.
- Regular reviews: Perform audits to ensure the system is maintained.
Sample 5S Workspace Layout
Step | Action | Benefit |
---|---|---|
Sort | Eliminate unneeded items | Less clutter, more focus |
Set in Order | Organize tools logically | Faster access to materials |
Shine | Maintain cleanliness | Improved safety and longevity of equipment |
Standardize | Set procedures and schedules | Consistency and stability in the workspace |
Sustain | Enforce regular audits | Ongoing improvements and engagement |
Choosing the Right Free 5S Course: What to Look for in Online Training
When selecting a free online 5S training course, it's crucial to assess the course content to ensure it aligns with your learning goals. You should focus on courses that offer practical, actionable insights rather than just theoretical knowledge. Understanding the principles behind the 5S methodology is important, but learning how to implement these principles effectively in your workplace is key for long-term success.
Another important factor is the course format and the delivery style. A course that includes interactive elements, such as quizzes, videos, and case studies, can enhance your learning experience. Additionally, you should look for a course that allows for self-paced learning, giving you the flexibility to digest the material at your own speed.
Key Features to Evaluate
- Course Structure: Check for a well-organized curriculum with clear learning objectives and progressive modules.
- Certification: Some free courses offer certificates upon completion, which may be useful for professional development.
- Instructor Expertise: Ensure the course is taught by experienced professionals or certified 5S practitioners who provide credible insights.
- Interactive Elements: Look for quizzes, real-world examples, or activities that encourage active participation.
- Reviews and Ratings: Student feedback can help gauge the quality and practicality of the course.
Course Comparison Table
Course Name | Length | Certification | Interactive Elements |
---|---|---|---|
Course A | 4 hours | Yes | Quizzes, Case Studies |
Course B | 6 hours | No | Videos, Discussion Forums |
Course C | 2 hours | Yes | Interactive Exercises, Real-world Examples |
“The most valuable aspect of a 5S training course is not just understanding the principles but being able to apply them effectively in real-world scenarios.”
How to Evaluate the Results of 5S After Completing Free Online Training
Measuring the impact of 5S implementation after completing free online training is crucial for ensuring that the concepts have been effectively understood and applied. This assessment helps identify both improvements and areas that need further attention. Various metrics and methods can be employed to evaluate success, ranging from qualitative feedback to quantitative data analysis.
After the training, you should focus on specific criteria to measure performance. These criteria might include productivity increases, safety improvements, and employee engagement levels. In addition, the actual application of the 5S principles should be observed in the workplace to ensure that they align with the theoretical knowledge gained during the course.
Key Indicators for Measuring Impact
- Productivity Gains: Assess whether employees are completing tasks more efficiently or faster due to streamlined processes.
- Safety Improvements: Check if the workplace is safer with reduced accidents or near misses.
- Employee Engagement: Evaluate whether employees show a greater sense of ownership and responsibility in maintaining the workspace.
- Waste Reduction: Measure the decrease in unnecessary materials, time, or effort.
Evaluation Methods
- Surveys and Feedback: Collect feedback from employees to gauge their understanding of the principles and the ease of applying them in real work scenarios.
- Workplace Audits: Conduct regular audits of the work environment to check if the 5S principles are being maintained.
- Key Performance Indicators (KPIs): Use KPIs like cycle time, inventory levels, and quality control metrics to track improvements over time.
Results Tracking Table
Metric | Before Training | After Training | Change (%) |
---|---|---|---|
Productivity | 85% | 90% | +5% |
Accidents | 10 | 4 | -60% |
Employee Engagement | 70% | 80% | +10% |
“Measuring impact is not just about numbers, but also about creating a culture of continuous improvement. Regular assessments ensure long-term success of the 5S methodology.”
Common Mistakes in 5S Implementation and How to Avoid Them
When implementing the 5S methodology, companies often encounter challenges that can derail the process. These mistakes can undermine the goals of 5S, resulting in a disorganized workplace and a lack of sustainable improvements. By recognizing and addressing these common pitfalls, businesses can ensure a successful implementation and achieve long-term benefits.
One of the key mistakes in 5S implementation is the failure to engage all team members in the process. Without the active participation of everyone, from top management to shop-floor workers, the system can quickly lose momentum. Another frequent issue is a lack of regular audits and follow-ups, which can lead to the deterioration of improvements made during the initial stages of the program.
Key Mistakes and How to Avoid Them
- Neglecting Employee Involvement: Ensuring that all team members understand the purpose of 5S and actively participate in the process is crucial. If the initiative is led only by a small group, others may not feel motivated to contribute.
- Lack of Continuous Improvement: Implementing 5S once and not revisiting or improving it leads to stagnation. Continuous monitoring and adjustments are necessary to maintain the effectiveness of the system.
- Skipping Standardization: Without a clear and standardized approach for maintaining cleanliness and organization, the gains from 5S can quickly slip away. The absence of consistent practices can cause confusion and disorder.
Steps to Overcome These Challenges
- Involve All Employees: Educate every team member about the benefits of 5S and how they can contribute to its success. Encourage open communication and feedback.
- Establish Regular Audits: Schedule frequent audits to ensure 5S principles are being followed and identify areas that need improvement.
- Standardize Practices: Create clear guidelines and procedures for maintaining a clean and organized workspace. Ensure that everyone adheres to these standards consistently.
“The success of 5S relies on continuous commitment and regular checks. It is a journey, not a one-time event.”
Mistake | Solution |
---|---|
Failure to engage all employees | Involve all team members in training and decision-making |
Lack of follow-ups | Schedule regular audits and check-ins |
Unclear standardization | Develop and implement clear, consistent guidelines |
How to Apply 5S Methodology in Everyday Tasks After Completing Online Training
After completing an online course on 5S, the challenge shifts to implementing the principles in daily workflows. The key to success is consistency and continuous improvement. In this article, we explore how to seamlessly integrate 5S techniques into routine operations to boost efficiency, organization, and workplace safety.
Integrating the 5S system into your daily operations can be achieved through structured steps. Below are practical suggestions for how to embed these principles into your work environment.
Steps to Implement 5S Principles in Daily Operations
- Sort: Identify and remove unnecessary items from the workspace. Establish clear criteria for keeping or discarding tools and materials.
- Set in Order: Organize essential items based on usage frequency. Create dedicated spaces for each tool to avoid clutter.
- Shine: Maintain cleanliness by assigning daily cleaning tasks and routines to ensure that workspaces are always tidy and operational.
- Standardize: Develop standard operating procedures (SOPs) that include 5S practices, making them part of regular work routines.
- Sustain: Regularly review progress, hold team meetings to reinforce practices, and ensure that all members adhere to the set standards.
Tracking Progress Through Regular Audits
To measure success, implement periodic audits to ensure 5S principles are maintained. These audits can be simple checklists or more thorough assessments, depending on the organization's needs.
Tip: Regular reviews help identify areas for improvement and reinforce the importance of 5S among all team members.
5S Principle | Daily Action | Review Frequency |
---|---|---|
Sort | Remove unnecessary items | Weekly |
Set in Order | Organize tools based on use | Daily |
Shine | Clean work areas and equipment | Daily |
Standardize | Update SOPs with 5S steps | Monthly |
Sustain | Conduct team meetings for reinforcement | Monthly |
Building a Culture of Continuous Improvement with 5S Techniques
The implementation of 5S techniques in an organization fosters a culture of ongoing improvement. By focusing on organization, cleanliness, and efficiency, these methods help streamline processes, minimize waste, and ensure that every team member contributes to a more productive environment. The continuous evaluation and refinement of workplace practices are essential for maintaining high standards and responding to challenges effectively.
5S is not just a one-time task; it requires regular monitoring and commitment to improvement. By instilling these principles into daily operations, companies can build a sustainable environment that encourages everyone to actively participate in maintaining standards and looking for new ways to enhance performance.
Key Elements of 5S Implementation
- Sort - Identify and remove unnecessary items from the workspace.
- Set in Order - Organize tools, materials, and resources for easy access.
- Shine - Regularly clean work areas to maintain high standards of hygiene.
- Standardize - Create processes and guidelines for maintaining organization.
- Sustain - Ensure consistent adherence to 5S practices over time.
Benefits of Cultivating a Continuous Improvement Culture
- Increased Efficiency: With an organized workspace, workers can find tools quickly, leading to faster task completion.
- Higher Morale: Employees feel empowered when they actively contribute to the upkeep of their environment.
- Reduced Waste: Unnecessary items are removed, leading to less clutter and more effective use of resources.
- Enhanced Safety: A cleaner, more organized workplace reduces the risk of accidents and injuries.
“Continuous improvement is not just about fixing problems, but also about anticipating potential issues and preventing them from arising.”
Tracking Progress with 5S
5S Step | Measurement Criteria | Improvement Actions |
---|---|---|
Sort | Number of items removed from the workspace | Regular audits to ensure only necessary items are kept |
Set in Order | Time taken to locate tools and materials | Reorganize layout based on team feedback |
Shine | Frequency of cleaning tasks | Implement a routine cleaning schedule |
Standardize | Consistency in following processes | Create visual aids and clear documentation |
Sustain | Adherence to 5S practices | Monitor and encourage team participation |